CrudeFlex: A new approach to crude processing flexibility & process optimization
Ever-changing market dynamics, such as food availability, financial incentives and quality changes, drive the continuous need for improved flexibility and proactive optimization efforts to reliably capitalize on production.
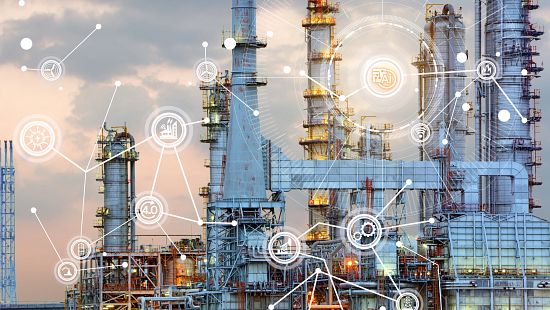
If refiners want to thrive in this increasingly challenging environment, they will need to improve or at least maintain current levels of unit reliability while successfully processing more diverse and opportunistic feedstock. The CrudeFlex Program helps refiners increase profitability like never before through a customized solution specific to the business objectives and needs of the Crude Unit. It gives refiners a higher level of system assurance, providing a radical improvement in the refinery's ability to mitigate and manage specific threats in the crude unit and wastewater operation.
This suite of automation tools provides refiners with greater levels of insight that can be used to respond to events in real time and identify the root cause of process upsets that would otherwise go unnoticed. Essentially, the increased volume of good data allows us to make intelligent, informed decisions while increasing unit reliability.

3D TRASAR™ Technology for Overhead Systems in Crude Oil Units (3DTCOS)
The Challenge: Processing conditions in the crude unit overhead system are constantly changing, driving the need for continuous on-line monitoring of process variables critical to corrosion simulation and a connected mitigation control system for maximum reliability.
3D TRASAR Technology For Crude Unit Top Systems is a comprehensive and advanced technology that leverages the information gathered by 3DTRASAR analyzers and connected chemistry to provide continuous and reliable data on top system chemistry conditions, enabling delivery of the right chemistry, in the right amount, at the right time, to reduce corrosion and improve crude unit reliability, while providing the ability to optimize tower operations to minimize the risk of salt formation and maximize unit yields.
- Operates 24/7 by monitoring critical parameters, highlighting events that would otherwise go unnoticed.
- It enables refiners to identify and mitigate threats before they advance, improving reliability and reducing the risk of unscheduled shutdowns.
- Improve flexibility in crude processing and adjust operational parameters to maximize profitability.
CASE STUDY AT LATAM REFINERY: FINDINGS OF SODA DEVIATIONS
BACKGROUND
A unit for corrosion control in the crude unit overhead system, 3DTCOS, has been operating since early 2021 in a Latin American Refinery, allowing to automatically detect, mitigate and correct process deviations that were not previously visible due to the frequency of the analytical routine, according to industry standards, but were observed through the unit's performance indexes.
The crude unit control system was proactively focused on desalting process improvements and reactively focused on chloride control at the top, through the dosing of caustic soda at the desalter outlet, along with the addition of neutralizing amine and filmic at the tower outlet to control pH and protect metallurgy.
The refinery had been working intensively with Ecolab to ensure proper soda dosing for the amount of total salts entering the tower, a challenging task considering that the control was carried out entirely manually. We will see how through 3DTCOS it was possible to increase the reliability of the unit, being able to detect acid incursions due to increases in chloride concentration at the top of the atmospheric tower of the crude unit, generated by deviations in the dosing of soda, associated with changes in crude qualities or operating conditions not identified by the analytical routine mentioned above.
By having real-time measurement of pH and Chlorides through 3DTCOS, it was possible to detect deviations in soda control that occurred in short periods of time, and together with our Pathfinder simulator allowed us to estimate that the fouling potential could increase by about 40% during these events. It is important to note that these events did not impact the unit as they could be detected by the automation system, 3DTCOS, and mitigation actions were managed in a timely manner.
SOLUTION
3DTCOS began monitoring in manual mode as part of the "learning phase", during which potential problems could be detected as manual changes occurred to improve performance. By migrating to automatic monitoring mode, performance against corrosion and fouling potential was further improved, as we will see below.
The graphs below show some events that were detected and corrected by 3DTCOS, thus improving pH and Chloride control in the overhead system:
Event 1: 3DTCOS learning stage: Soda and amine control in manual mode. Soda underdosing during the weekend
Event during the weekend, occurred during the 3DTCOS learning stage. Soda under-injection occurs and since the automatic neutralizer control is not activated because it is in the implementation stage, the pH drops until it reaches values around 4 and is corrected with the corresponding adjustment in the soda injection after the event has started. Thanks to 3DTCOS it was possible to identify this alteration of the process and to show the response times in manual mode.

Event 2: 3DTCOS in automatic mode for pH-linked neutralizing amine control. Soda underdosing
During this event, reprocess crude was being handled, with an eventual higher water/emulsion content. Therefore, there was a high potential for stabilization of the emulsion band in the desalter, making the system more susceptible. This condition generated that the continuity of the adjustment in the soda dosage became even more important to ensure the protection of the system, since it is the last barrier to avoid the formation of HCl in the top system.
In the face of these unfavorable conditions, thanks to 3DTCOS it was possible to identify in real time the drop in pH and increase in chlorides. The 3DTCOS equipment exercised control, working in automatic mode, immediately increasing the dose of neutralizing amine, mitigating the effect of the event.

In summary, through 3DTCOS it was possible to identify operational deviations that occur 10% of the time and generate 90% of the corrosion and fouling problems.
CrudeFlex technology makes it possible to identify and correct process deviations in real time, in addition to generating a failure history of unforeseen events and providing valuable information to trigger the necessary improvements in the operation in the short, medium and long term, as appropriate.
